The Lycoming instructions are conflicting, I think.
If using the 'fish scale' technique and applying 14 lbs as described and getting 5/16" deflection, the torque required to rotate the alternator pulley is 30 in-lbs.
According to the 'torque' method shown, the torque required to rotate the pulley is 22 ft-lbs!
I tried to get the belt tight enough to achieve 22 ft-lbs and with the belt stretched as tight as I could get with a prying crowbar, I could only get 12 ft-lbs and the belt was tight as a drum.
Does anybody have an explanation for this apparent contradiction?
I sent Lycoming a message with the same question.
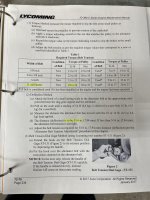
If using the 'fish scale' technique and applying 14 lbs as described and getting 5/16" deflection, the torque required to rotate the alternator pulley is 30 in-lbs.
According to the 'torque' method shown, the torque required to rotate the pulley is 22 ft-lbs!
I tried to get the belt tight enough to achieve 22 ft-lbs and with the belt stretched as tight as I could get with a prying crowbar, I could only get 12 ft-lbs and the belt was tight as a drum.
Does anybody have an explanation for this apparent contradiction?
I sent Lycoming a message with the same question.
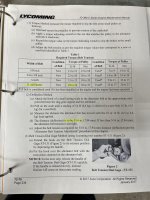
Last edited: