Finished the primer for the bodywork on the lower cowl. Next step is sanding with #400, then epoxy primer surfacer over entire piece, sand flat, then epoxy primer and paint.
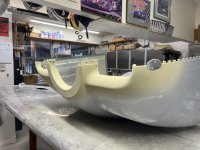
I didn't like how the oil door fit the opening very well, so I adjusted the surrounding cowl to match the elevation better, finished bodywork and primed.
Now, this piece is ready for #400 sanding, epoxy primer surfacer, primer and paint.

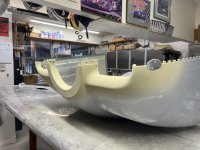
I didn't like how the oil door fit the opening very well, so I adjusted the surrounding cowl to match the elevation better, finished bodywork and primed.
Now, this piece is ready for #400 sanding, epoxy primer surfacer, primer and paint.
