[email protected]
I'm New Here
I screwed up and set the rivets connecting the VS-1012 rudder hinge brackets before setting the two rivets between the brackets that connect only the VS 1017 doubler and the VS-1003 rear spar. Not sure I can effectively get a bucking bar or rivet set in between the brackets.... though I am open to suggestions.
Has anyone used pull rivets for those two?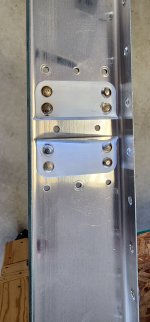
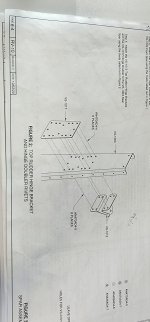
Has anyone used pull rivets for those two?
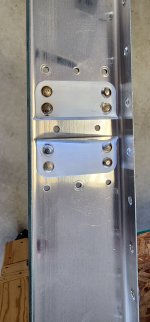
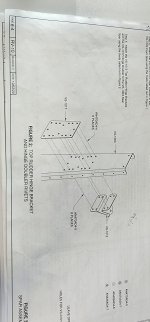