Hello there, I'm planning to scratch build a -6, I'm currently drawing all the plans in CAD to make sure that I understood them before start cutting any metal
The builder manual says about forming the wing ribs but I can't find some details and measurements like flanges length, radius and depth, if someone can give-me some help I'll be very thankfull
I'm also searching for olds threads of someone who plans built a RV6 (or a -3, -4 for reference) any informations is welcome, thanks
The builder manual says about forming the wing ribs but I can't find some details and measurements like flanges length, radius and depth, if someone can give-me some help I'll be very thankfull
I'm also searching for olds threads of someone who plans built a RV6 (or a -3, -4 for reference) any informations is welcome, thanks
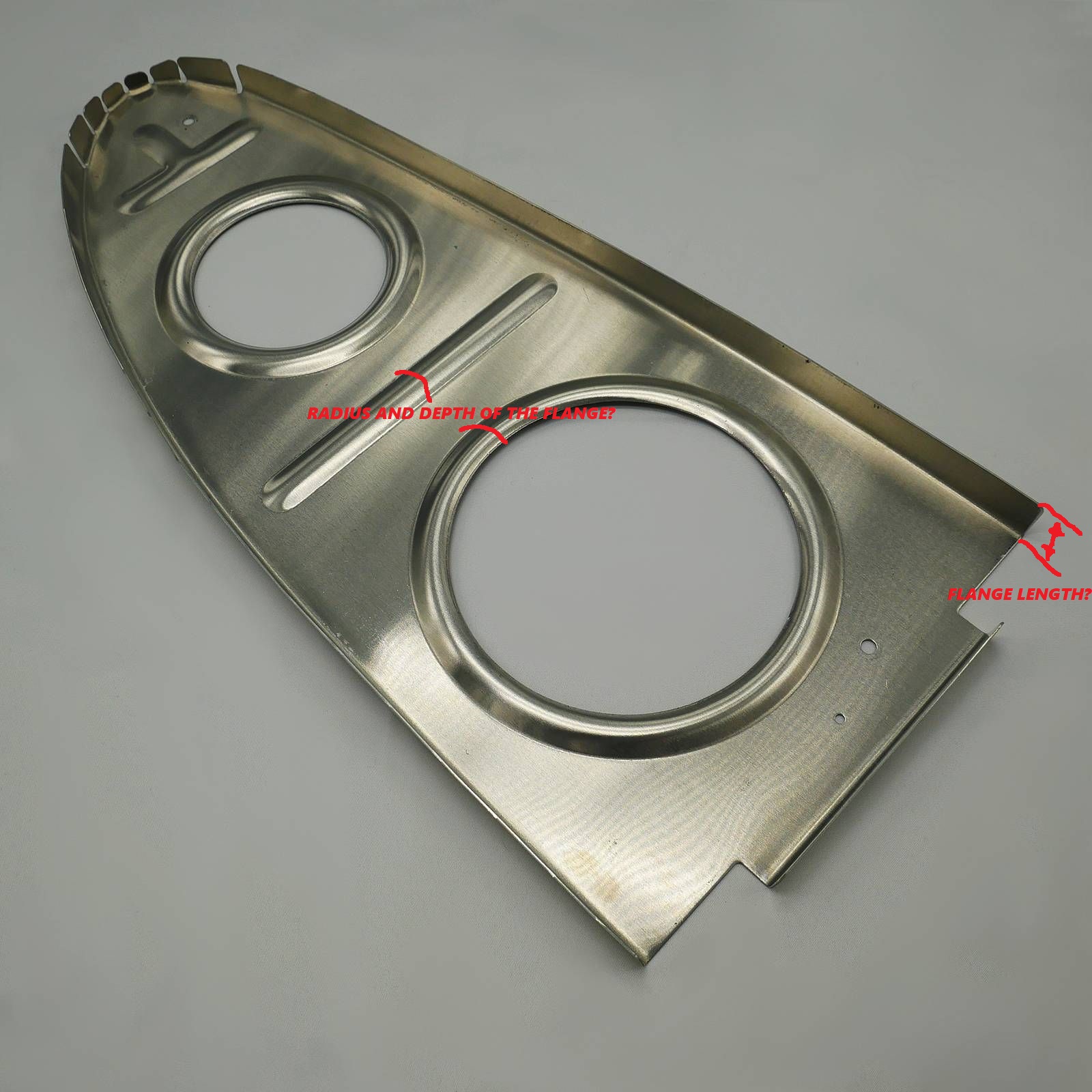