wirejock
Well Known Member
The Vans fairing isn't perfect, but most of it is usable by cutting the flanges that fit on top of the HS. I will adjust them to fit then reattach them. That leaves the bottom fairing. Sorry Vans. I can do better than a strip of aluminum angle.
Sweetie is a Potter. I've worked a lot of clay. Laying up a clay mold seemed the easiest. I taped everything off and applied a wedge of kids modeling clay in the corner from leading edge to trailing edge. Then I shaped it using a 2" hunk of PVC for the radius and a spray bottle with water. Easy peasy. It's not reusable, but only took a couple hours to tape and layup both molds. It needs to dry enough to apply more tape then I can layup the bottom fairing. <fingers crossed>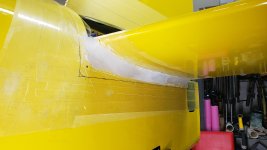
Sweetie is a Potter. I've worked a lot of clay. Laying up a clay mold seemed the easiest. I taped everything off and applied a wedge of kids modeling clay in the corner from leading edge to trailing edge. Then I shaped it using a 2" hunk of PVC for the radius and a spray bottle with water. Easy peasy. It's not reusable, but only took a couple hours to tape and layup both molds. It needs to dry enough to apply more tape then I can layup the bottom fairing. <fingers crossed>
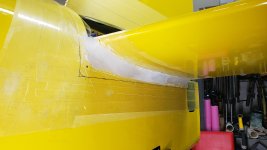