N941WR
Legacy Member
We have had a number of customers ask about the E/Pmag timing advance and how it works. I thought it might be worth posting our reply on here so that other Emag customers might benefit.
E/Pmag Electronic Ignition
The E/Pmag controls the ignition timing through a combination of:
1. Static timing of the E/Pmags set mechanically to approx 25 Deg (for typical Lycoming 4 cylinder)
2. Advance Curve Selected (e.g. Via the "A" or "B" configuration - or user configuration, if using the Laptop EICAD program or the Electronic Ignition Commander. The “B” curve is the only configurable curve and can be adjust as the user sees fit. The EICommander[/url’] stores multiple configurations and when sent to the E/Pmas updates the “B” configuration memory location.)
3. Amount of RPM and Manifold Pressure sensed
Typically, the E/Pmag static timing is mechanically set to around 20 deg BTDC using the Pmag set up procedures (blow in the tube or by turning the E/Pmags). A base table is then used to relate the rpm/manifold pressure values to the advance curve selected to provide the timing advance increase. So total advance = Static (25 deg BTDC) + advance value (function of RPM/Manifold pressure). The "A" advance curve is shown in orange line in the graph below. More aggressive advance curves are indicated in blue and less aggressive in Green. Note that if a very aggressive advance curve is configured and sent to the E/Pmags, you will hit the 39 Deg Max Angle shown at a lower RPM value.
The default factor advance curve is set by the "A" configuration which has a constellation shift of zero deg. This means the constellation shift = 0.0 which results in the active advance curve being the default "A" configuration curve. If the "B" curve is selected, then the advance curve is biased 5 deg in front(ahead of) the "A" curve as shown by the blue line in the drawing. So this is a more aggressive ignition advance as it will have approximately a five (5) degree timing advance over the “A” configuration at each rpm/manifold pressure point along the curve.
In either case as RPM/Manifold pressure changes this causes the total ignition advance to vary. Total Advance = Static Timing (20 Deg BTDC) + Amount of advance as a function of RPM/Manifold Pressure.
If you are using your Laptop and the Emag EICAD program provided from Emag’s web site or the EICommander to monitor, control or change your E/Pmag ignition configuration, there are a total of four ignition advance values affecting ignition timing. Two are static (limit) settings and two are dynamic values. All four items are reported over the E/Pmag serial communication link.
Static Advance Settings (These values can be adjusted with Laptop or EICommander)
1. Advance Maximum - This is the total ignition advance limit set by the configuration of the Pmag. Once and if this limit is reached, the Pmag will not advance the ignition timing beyond this value
2. Constellation Shift - This sets the aggressiveness of the advance curve. "A" is the default with constellation shift set = 0.0. "B" provides slightly more aggressive advance curve of being 5 degrees more advanced at each RPM/Manifold point than the "A" curve. The E/Pmag permits a maximum of +12.6 degree of “shift” - a very aggressive advance profile (negative values are also permitted, which might be desired for forced induction engines [turbo or super charging]).
These two settings place limits on maximum advance permitted and how aggressive the curve to that maximum advance will be. With a "B" curve for example the E/Pmag could reach the same point at a lower rpm/manifold pressure point than the "A" curve, so the ignition could run into the Maximum Advance limit at a lower rpm for example - unless the user adjusted the Maximum Advance Limit upward. Also the Maximum RPM limit for the E/Pmag may need to be increased to accommodate the more aggressive advance curve.
Dynamic Advance Values (These values are reported on the serial link by the E/Pmag)
1. Target Advance - exists and is reported over serial link, but not currently used nor displayed by the EICAD program or the EICommander.
2. Current Advance - this is the firing point of the E/Pmag - This is the total advance, which is a combination of the static timing point plus the timing advance based on the advance curve selected (A or B or user) and the point on that curve as a function of RPM/Manifold pressure.
E/Pmag Electronic Ignition
The E/Pmag controls the ignition timing through a combination of:
1. Static timing of the E/Pmags set mechanically to approx 25 Deg (for typical Lycoming 4 cylinder)
2. Advance Curve Selected (e.g. Via the "A" or "B" configuration - or user configuration, if using the Laptop EICAD program or the Electronic Ignition Commander. The “B” curve is the only configurable curve and can be adjust as the user sees fit. The EICommander[/url’] stores multiple configurations and when sent to the E/Pmas updates the “B” configuration memory location.)
3. Amount of RPM and Manifold Pressure sensed
Typically, the E/Pmag static timing is mechanically set to around 20 deg BTDC using the Pmag set up procedures (blow in the tube or by turning the E/Pmags). A base table is then used to relate the rpm/manifold pressure values to the advance curve selected to provide the timing advance increase. So total advance = Static (25 deg BTDC) + advance value (function of RPM/Manifold pressure). The "A" advance curve is shown in orange line in the graph below. More aggressive advance curves are indicated in blue and less aggressive in Green. Note that if a very aggressive advance curve is configured and sent to the E/Pmags, you will hit the 39 Deg Max Angle shown at a lower RPM value.
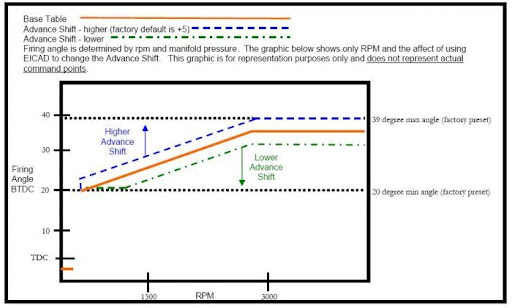
The default factor advance curve is set by the "A" configuration which has a constellation shift of zero deg. This means the constellation shift = 0.0 which results in the active advance curve being the default "A" configuration curve. If the "B" curve is selected, then the advance curve is biased 5 deg in front(ahead of) the "A" curve as shown by the blue line in the drawing. So this is a more aggressive ignition advance as it will have approximately a five (5) degree timing advance over the “A” configuration at each rpm/manifold pressure point along the curve.
In either case as RPM/Manifold pressure changes this causes the total ignition advance to vary. Total Advance = Static Timing (20 Deg BTDC) + Amount of advance as a function of RPM/Manifold Pressure.
If you are using your Laptop and the Emag EICAD program provided from Emag’s web site or the EICommander to monitor, control or change your E/Pmag ignition configuration, there are a total of four ignition advance values affecting ignition timing. Two are static (limit) settings and two are dynamic values. All four items are reported over the E/Pmag serial communication link.
Static Advance Settings (These values can be adjusted with Laptop or EICommander)
1. Advance Maximum - This is the total ignition advance limit set by the configuration of the Pmag. Once and if this limit is reached, the Pmag will not advance the ignition timing beyond this value
2. Constellation Shift - This sets the aggressiveness of the advance curve. "A" is the default with constellation shift set = 0.0. "B" provides slightly more aggressive advance curve of being 5 degrees more advanced at each RPM/Manifold point than the "A" curve. The E/Pmag permits a maximum of +12.6 degree of “shift” - a very aggressive advance profile (negative values are also permitted, which might be desired for forced induction engines [turbo or super charging]).
These two settings place limits on maximum advance permitted and how aggressive the curve to that maximum advance will be. With a "B" curve for example the E/Pmag could reach the same point at a lower rpm/manifold pressure point than the "A" curve, so the ignition could run into the Maximum Advance limit at a lower rpm for example - unless the user adjusted the Maximum Advance Limit upward. Also the Maximum RPM limit for the E/Pmag may need to be increased to accommodate the more aggressive advance curve.
Dynamic Advance Values (These values are reported on the serial link by the E/Pmag)
1. Target Advance - exists and is reported over serial link, but not currently used nor displayed by the EICAD program or the EICommander.
2. Current Advance - this is the firing point of the E/Pmag - This is the total advance, which is a combination of the static timing point plus the timing advance based on the advance curve selected (A or B or user) and the point on that curve as a function of RPM/Manifold pressure.
Last edited: