Clouddancer
Well Known Member
We planned to use an existing crossover-exhaust that was previously fitted on another RV-4. It suits us well, because both crossover pipes are in front of the oil sump and keeps us the space behind the oil sump free of exhaust pipes. The todays Vetterman crossover exghaust has one pipe in front and one behind the oil sump.
As you can see in the pictures below the exhaust pipes have low clearance in some places.
- Pic 1: approx. 0.12 Inch between each other and between a pipe and the oil sump
- Pic 2: approx. 0.16 Inch between the pipe and the oil fitting (used for inverted oil system)
For those having experience with similar installations: is this too close? Especially the clearance between the pipe and the fitting? There is no space to place a heat shield in between.
Thanks for your advice
As you can see in the pictures below the exhaust pipes have low clearance in some places.
- Pic 1: approx. 0.12 Inch between each other and between a pipe and the oil sump
- Pic 2: approx. 0.16 Inch between the pipe and the oil fitting (used for inverted oil system)
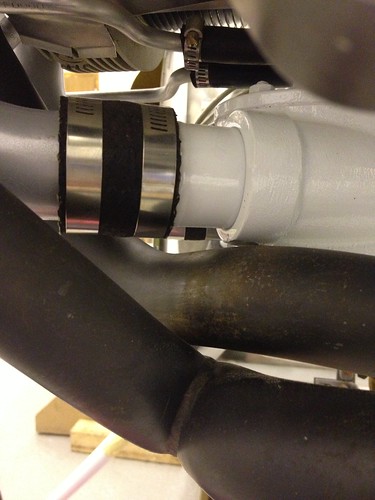
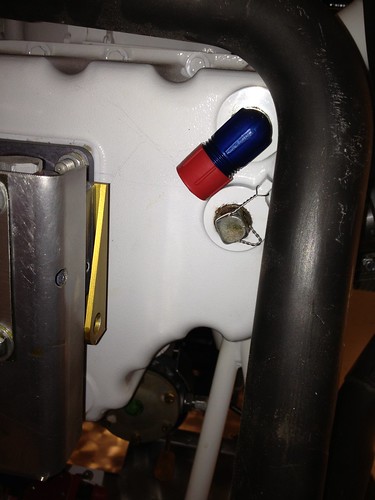
For those having experience with similar installations: is this too close? Especially the clearance between the pipe and the fitting? There is no space to place a heat shield in between.
Thanks for your advice