bryanhorgan
Member
After TONS of research, both anecdotal and documented, I'm having a hard time deciding whether or not Rec90 would work fine in a 0-360 with a 8.5 to 1 Compression ratio.
I know the safe answer is NO, just buy 100LL! But as a thought exercise (and the fact that I'm about to put 800+ hours on my airplane) I'd like to get past that.
While ethanol containing fuels may work, it seems there are many issues that may or may not crop up: water contamination, aluminum corrosion, rubber seals that you may or may not know about, etc. For that reason I'd like to focus on the ethanol free ones. For me, in Florida, that leaves the best available choice being Rec90.
Rec90 has an AKI rating of 90. Yes I spoke to the distributor, yes it's AKI. Lycoming's charts say an 0-360 with an 8.5 to 1 Compression ratio must have a minimum of 93 octane AKI (Lycoming Service Instruction 1070AB). Strangely Lycoming has 91 AKI on the chart, even though not 1 engine is approved for it.
BUT, according to ANY octane vs compression ratio chart I've been able to find (see below), a compression ratio of 8.5 only requires about 85 octane. Anything over that is "wasted" octane. The chart below is from energy.gov and details recommended octane ratings from auto manufacturers for specific vehicles' compression ratios over the last 90 years.
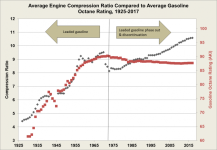
This leads me to wonder why 93, and not 85 octane is the approved fuel. It also makes me wonder if 3 octane rating will make any significant difference in an 0-360 8.5 to 1 Compression Engine.
I know the safe answer is NO, just buy 100LL! But as a thought exercise (and the fact that I'm about to put 800+ hours on my airplane) I'd like to get past that.
While ethanol containing fuels may work, it seems there are many issues that may or may not crop up: water contamination, aluminum corrosion, rubber seals that you may or may not know about, etc. For that reason I'd like to focus on the ethanol free ones. For me, in Florida, that leaves the best available choice being Rec90.
Rec90 has an AKI rating of 90. Yes I spoke to the distributor, yes it's AKI. Lycoming's charts say an 0-360 with an 8.5 to 1 Compression ratio must have a minimum of 93 octane AKI (Lycoming Service Instruction 1070AB). Strangely Lycoming has 91 AKI on the chart, even though not 1 engine is approved for it.
BUT, according to ANY octane vs compression ratio chart I've been able to find (see below), a compression ratio of 8.5 only requires about 85 octane. Anything over that is "wasted" octane. The chart below is from energy.gov and details recommended octane ratings from auto manufacturers for specific vehicles' compression ratios over the last 90 years.
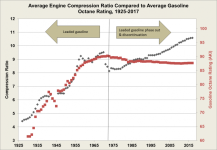
This leads me to wonder why 93, and not 85 octane is the approved fuel. It also makes me wonder if 3 octane rating will make any significant difference in an 0-360 8.5 to 1 Compression Engine.