While closing the last bay of of the bottom skin of the wing while in its cradle the bucking bar fell (fatigue) through the holes in the spar and perforated the leading edge as seen in the pictures.
Defect was "drilled out" finally with a unit to 3/4 inch diameter. After exploring repair options I have come up with the doubler shown however I battling with a filler.
No response from vans support despite two attempts. Friend has subsisted "Bondo" I thought some fiberglass resin. Does anyone have a reliable suggestion or resource that addresses this specific problem. A 3/4" diameter aluminum 2024-T3 filler will buckle if attempting to rivet to this doubler. Any suggestions would be appreciated.
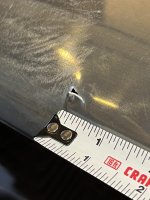
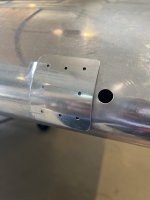
Defect was "drilled out" finally with a unit to 3/4 inch diameter. After exploring repair options I have come up with the doubler shown however I battling with a filler.
No response from vans support despite two attempts. Friend has subsisted "Bondo" I thought some fiberglass resin. Does anyone have a reliable suggestion or resource that addresses this specific problem. A 3/4" diameter aluminum 2024-T3 filler will buckle if attempting to rivet to this doubler. Any suggestions would be appreciated.
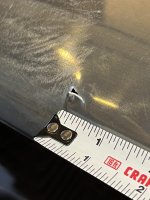
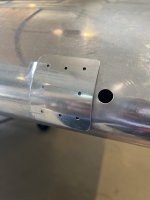