The fitting on the left (the black one) is a restrictor fitting i bought from ACS for the oil pressure port on my O-320.
The engine came from Aero Sport with the fitting on the right. That fitting does not have the obvious pinhole restriction on the pipe-thread end like the black one does, but it does appear to have somewhat of a restriction on the flared end. Are these just different types of restrictor fittings, both equally suitable for the oil pressure port?
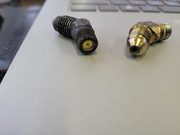
The engine came from Aero Sport with the fitting on the right. That fitting does not have the obvious pinhole restriction on the pipe-thread end like the black one does, but it does appear to have somewhat of a restriction on the flared end. Are these just different types of restrictor fittings, both equally suitable for the oil pressure port?
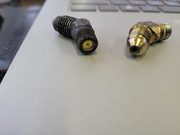