RudiGreyling
Well Known Member
Hi Everyone,
I thought I?d share my tip on quicker drilling the spar (RV7 in this case) for the tank plate nuts. Lots of people experience problems when countersinking the spar, since the hole gets too big for the pilot hole and start to go oval or chatter. I did a lot of research and a lot of people make single nutplate/spar jigs, then move them to each hole, but that takes way too long.
I borrowed some ideas from others and improved on them. This tip should save you lot of time if you have the correct tools. If you have further improvements or tips please post them below to consolidate all the spar drilling tips.
Kind Regards
Rudi
Required Tools:
Masking tape the top gap between the spar and spar flange in order to eliminate any shavings going in there.
2) Take your high speed air drill and final drill all the #19 size holes from the top through the spar through the aluminium angle. Keep it steady, it will take a small effort to get through the aluminium angle stock.
3) Take a high torque battery operated drill, and countersinks all the #19 holes with your #19 countersink. I prefer the battery operated drill on the big countersink holes because the torque is linear with the speed control and produced less chatter than my electric drill and my high speed air drill does not have enough torque.
4) The Countersink instructions for the spar can be found in the RVator : 2005, First Issue, page 10
RVator:
Update: 10 Aug 2005 with RVator countersink instructions
I thought I?d share my tip on quicker drilling the spar (RV7 in this case) for the tank plate nuts. Lots of people experience problems when countersinking the spar, since the hole gets too big for the pilot hole and start to go oval or chatter. I did a lot of research and a lot of people make single nutplate/spar jigs, then move them to each hole, but that takes way too long.
I borrowed some ideas from others and improved on them. This tip should save you lot of time if you have the correct tools. If you have further improvements or tips please post them below to consolidate all the spar drilling tips.
Kind Regards
Rudi
Required Tools:
- #19 Pilot Countersink - 3 flute cutter (got mine from Cleaveland tools as part of their RV package)
- Stock Aluminium Angle 1/16 to 1/8 thick
- Battery operated drill
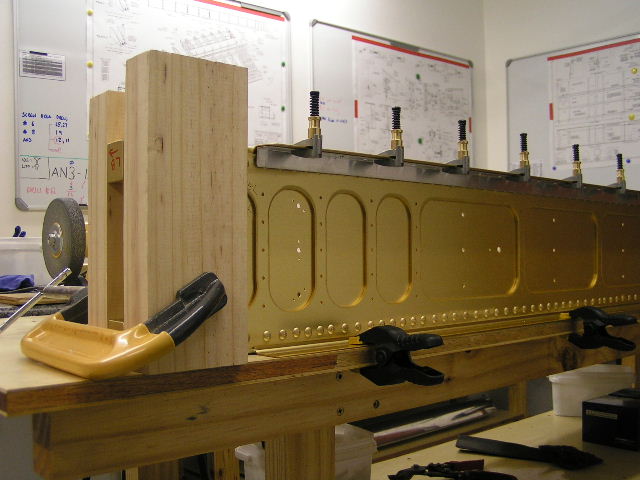
Masking tape the top gap between the spar and spar flange in order to eliminate any shavings going in there.
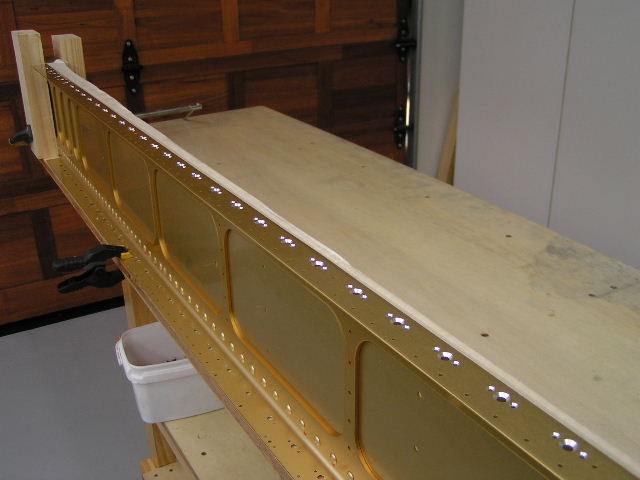
2) Take your high speed air drill and final drill all the #19 size holes from the top through the spar through the aluminium angle. Keep it steady, it will take a small effort to get through the aluminium angle stock.
3) Take a high torque battery operated drill, and countersinks all the #19 holes with your #19 countersink. I prefer the battery operated drill on the big countersink holes because the torque is linear with the speed control and produced less chatter than my electric drill and my high speed air drill does not have enough torque.
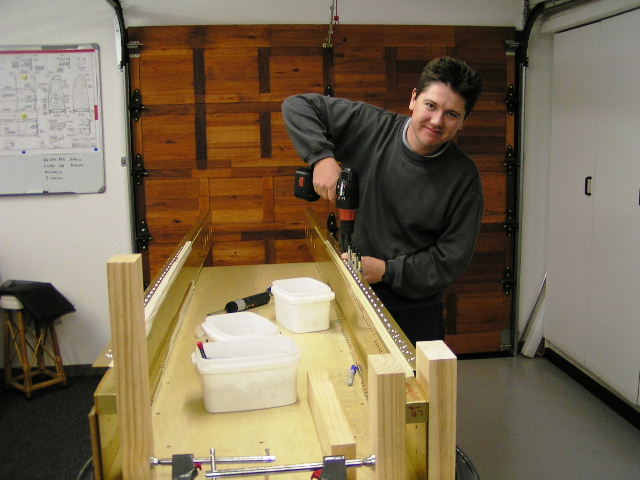
4) The Countersink instructions for the spar can be found in the RVator : 2005, First Issue, page 10
RVator:
Continue on next Post......We countersink until the top of the screw is level with the surface, then go 2 clicks deeper on the microstop. The actual outside diameter of the countersink measures .365 to .375"
Update: 10 Aug 2005 with RVator countersink instructions
Last edited: