aarvig
Well Known Member
I have sent these photos to Vans but I thought I would post here as well to see if anyone out there has experienced this. I am attaching my wing ribs to my wing spar on my 9A. On the inboard 11 ribs there is a doubler that is a preassembled component on the wing spar. The rib attaches to the doubler then the wing spar and the whole thing is riveted together. On those ribs I did not have any cracking on the wing spar web. On the outboard 3 ribs (didn't attach the outboard rib yet per instructions) there is no doubler. It is just rib riveted to the wing spar. On those ribs there is a "spider web" looking series of cracks emanating from the hole. There is primer under the rivet (that is the gray stuff you see around the rivet), the holes have been deburred. Is this normal and why is it happening? I used a 3X rivet gun with an offset rivet set. Due to the offset set the gun was set at 55 psi.
The first two pictures are of the outboard 3 ribs without the doubler. The last picture is of one of the inboard 11 ribs that has the doubler.
The first two pictures are of the outboard 3 ribs without the doubler. The last picture is of one of the inboard 11 ribs that has the doubler.
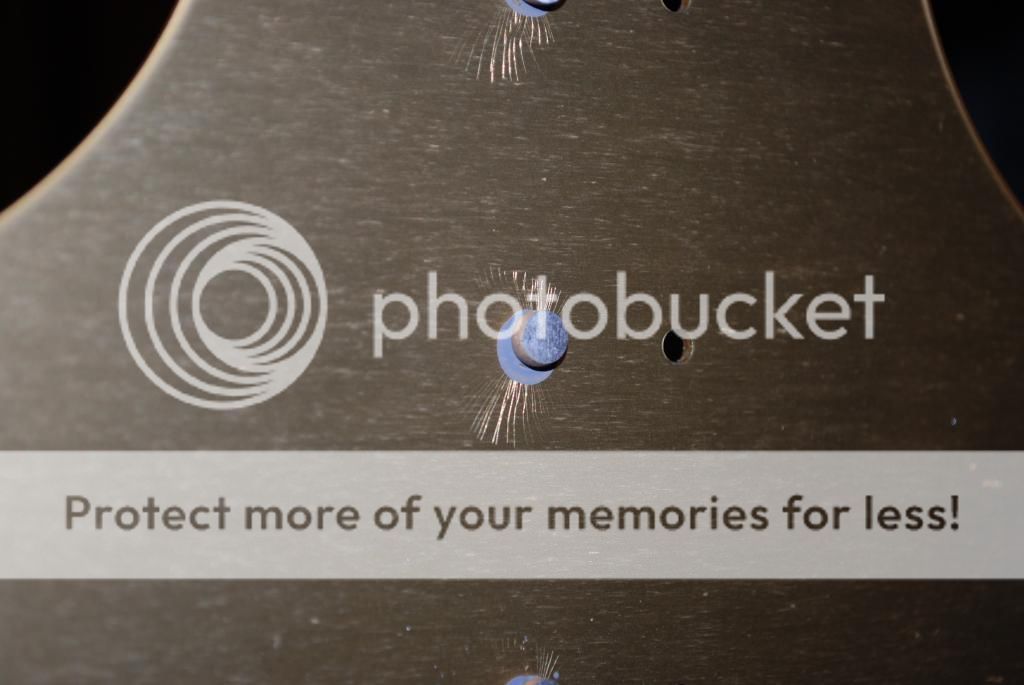
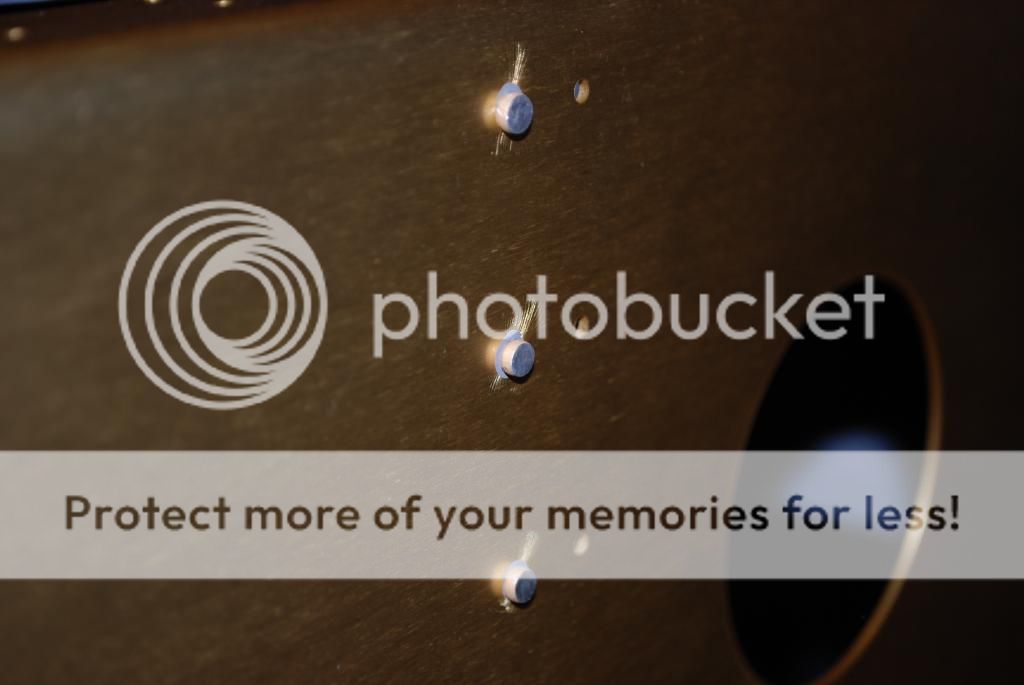
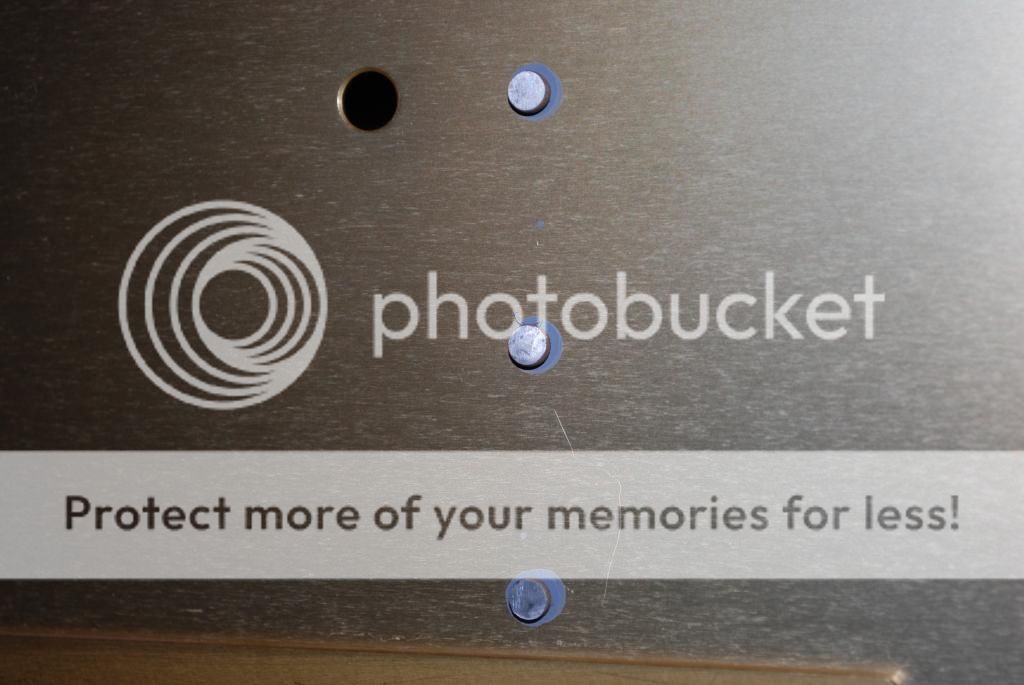
Last edited: