Mark Wright
Member
Is there any benefit, or has anyone tried adding additional baffling as shown in the pic below? This is just a mock up, and the final would seal around the lifter tubes and the fuel injector lines and extend up to the plenum. I have not done a flow analysis of this idea yet, but just looking at it, it seems that it would help eliminate the turbulent air over the center portion of the engine, and direct the airflow where it needs to go. Carbon fiber with high temp epoxy would work. Is there any data concerning the temp of the cylinders at the base?? It wouldn't be nearly as high as the cht of course.
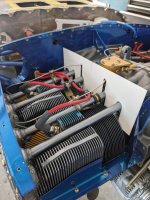
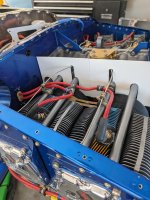
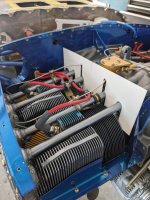
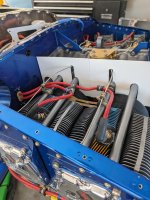